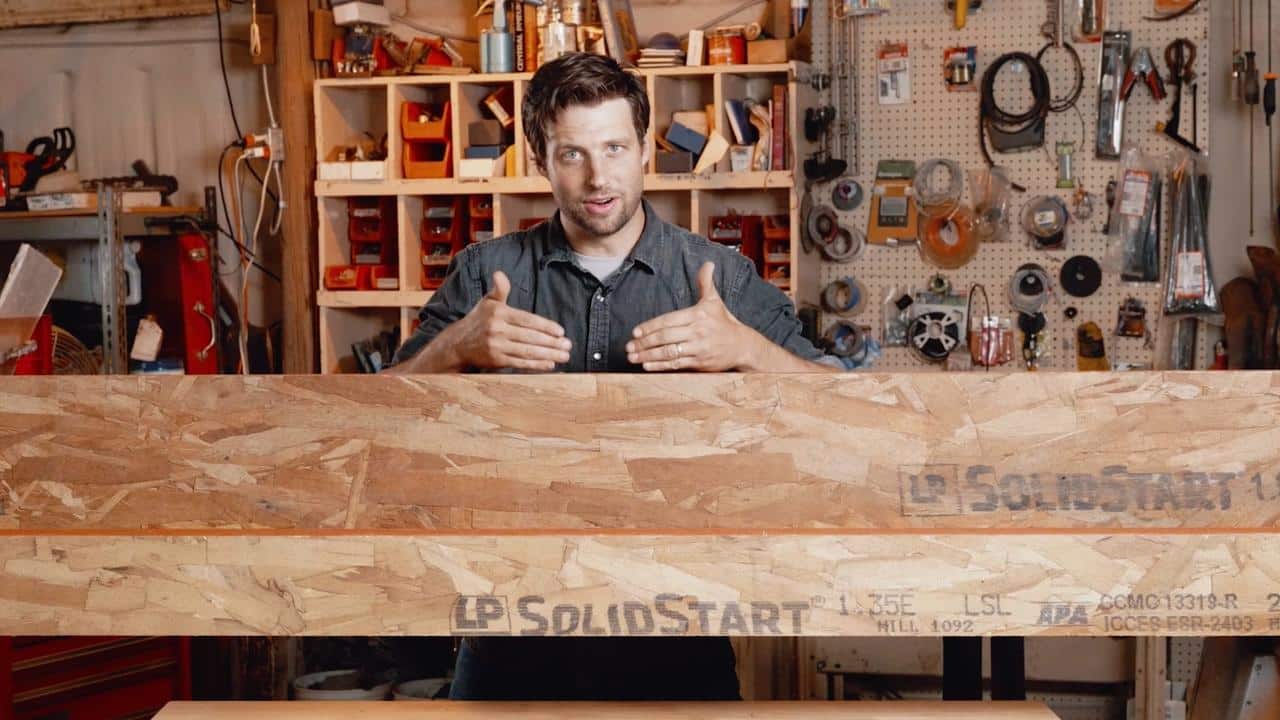
Engineered wood boards are generally made from the same hardwoods and softwoods used to manufacture lumber, but mixed with additives like adhesives. This type of wood often utilizes waste wood from sawmills, and are treated through chemical or heat processes to produce wood that meets size requirements that are hard to find in nature.
Engineered wood is used in a variety of applications, from home construction to commercial buildings to industrial products.
“Engineered lumber is lumber that although it comes from wood, it’s been processed to be something slightly different and perform in a different, oftentimes better way than what just the raw wood would perform.” -Professional builder Jordan Smith
7 Popular Types of Engineered Wood
Engineered wood products are available as framing members—beams, for example—and sheet goods, which can be used as sheathing or flooring.
1. Laminated Veneer Lumber (LVL)
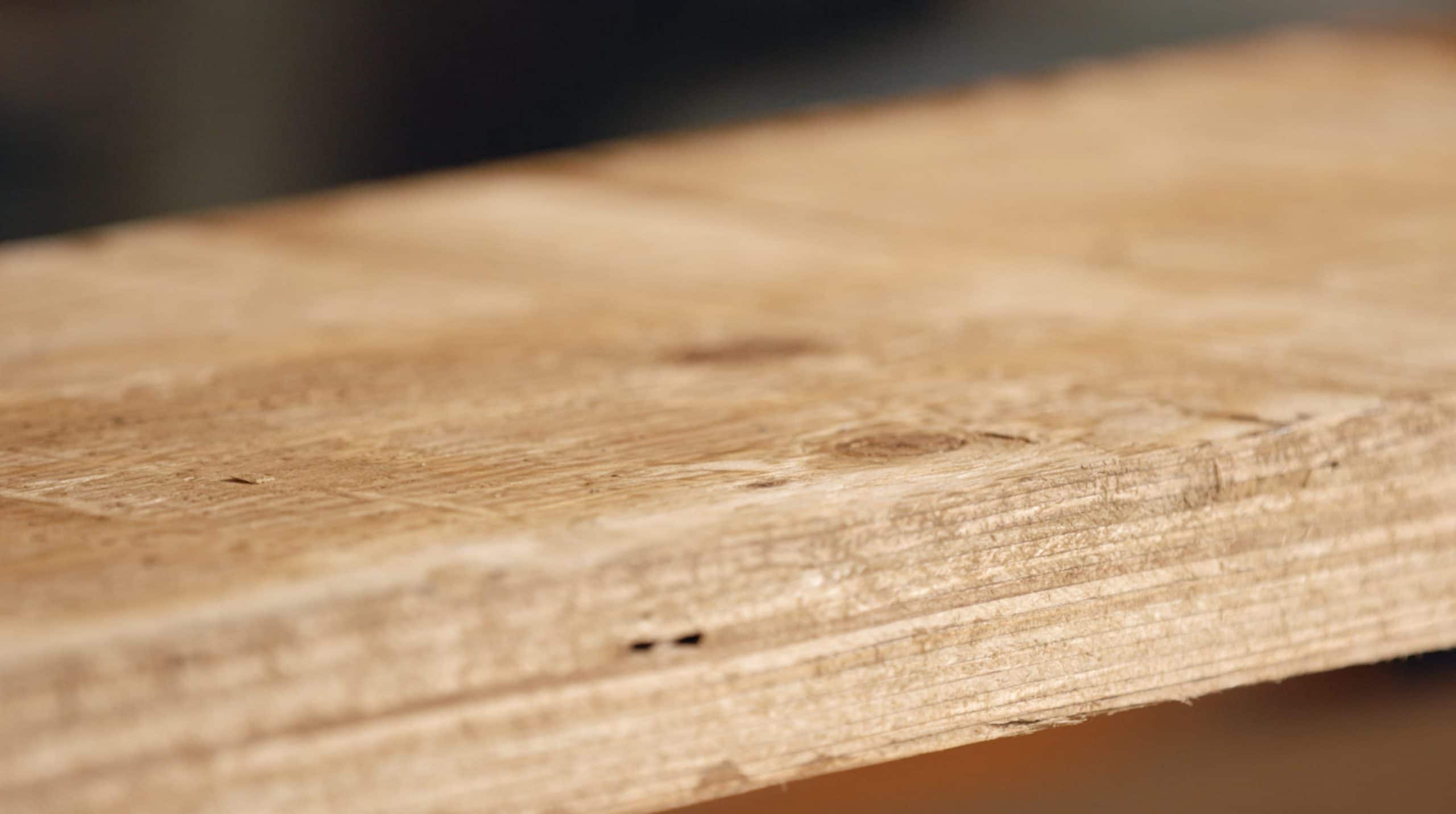
Made of wood veneers that are compressed together with resins and glues, LVL is a high density engineered wood product used in framing. LVL is very strong, but has only one strength axis, because its veneers are stacked with the grain running in the same direction. This means you can only load LVL in one direction.
2. Laminated Strand Lumber (LSL)
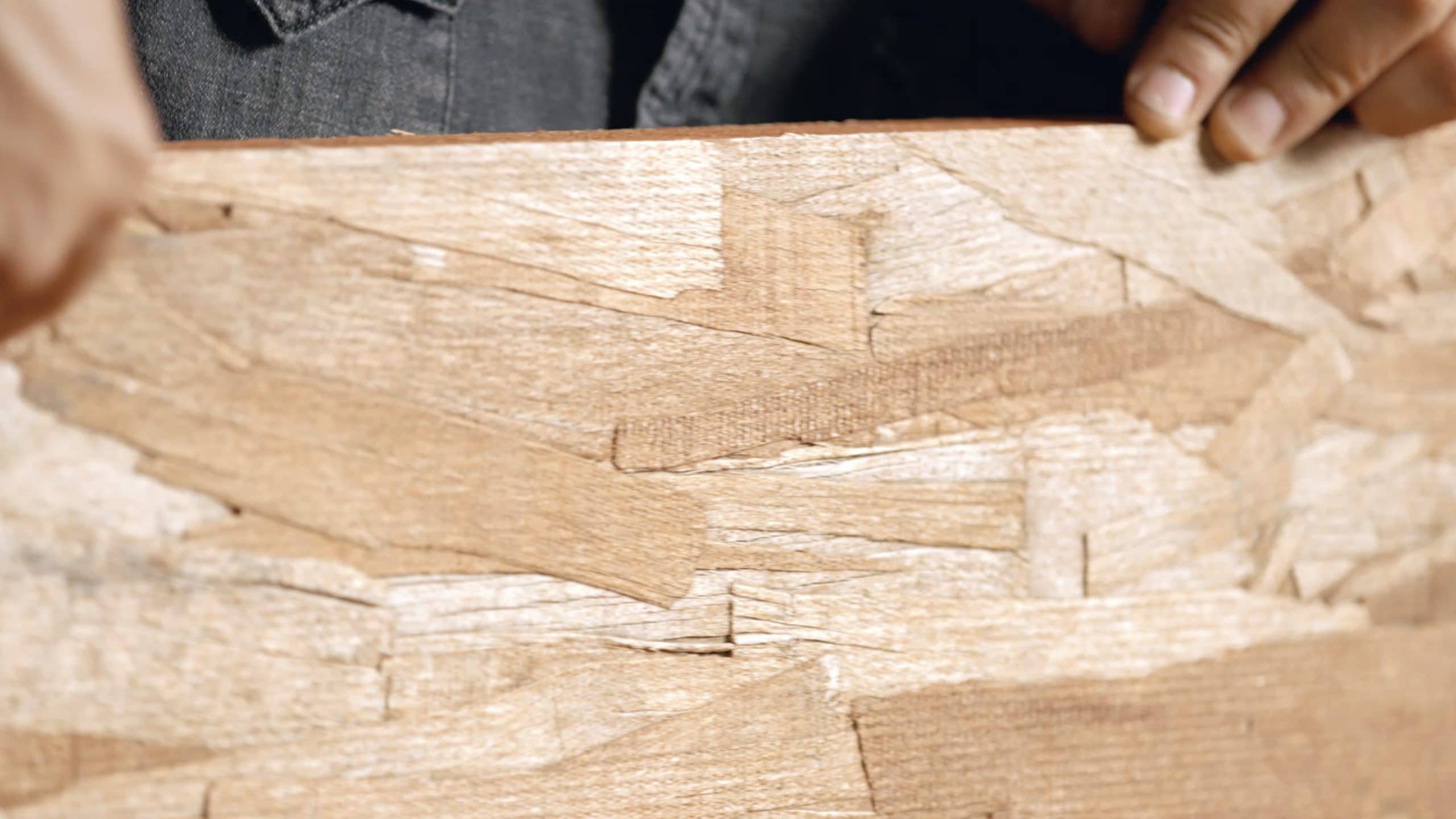
Made of small strips of wood—strands—that are placed in a dense, angled pattern, LSL is a high quality engineered wood product that can be an even higher density and stronger than LVL. It is composed of about 95% wood fiber and 5% resin. LSL is very resistant to weight and torsion because of the angled pattern in which the wood strips are placed. LSL is also expensive—it’s about 3x the cost of dimensional lumber.
3. Oriented strand board (OSB)
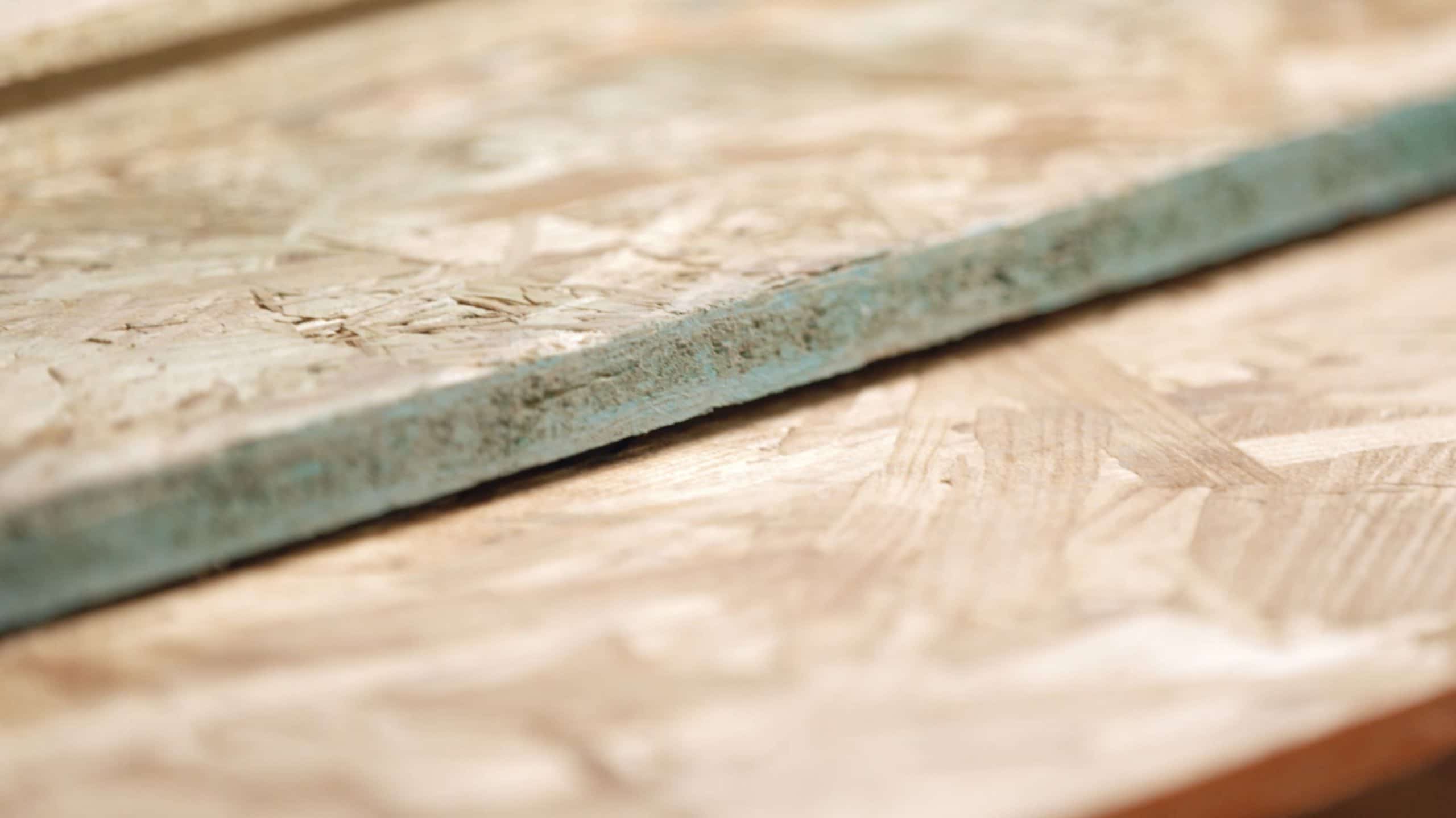
This type of sheet good is formed by combining wood strands or flakes with adhesives and then compressing them. It is manufactured in wide mats and is good for load-bearing applications such as flooring and roof decking. All OSB isn’t created equal—some is sanded (like Advantech or Legacy premium subfloor), and other boards are not. Some OSB is moisture resistant, other boards are not. Make sure that you are using premium grade OSB if there’s any chance of it experiencing whether.
It is important to note that for OSB (and plywood), you want to gap all of your ends, so that when it expands and contracts with moisture in the long direction, you aren’t causing it to buckle. However, on the tongue and groove of premium subflooring, there is a pre-manufactured stop that gives you the ⅛-inch gap in between boards.
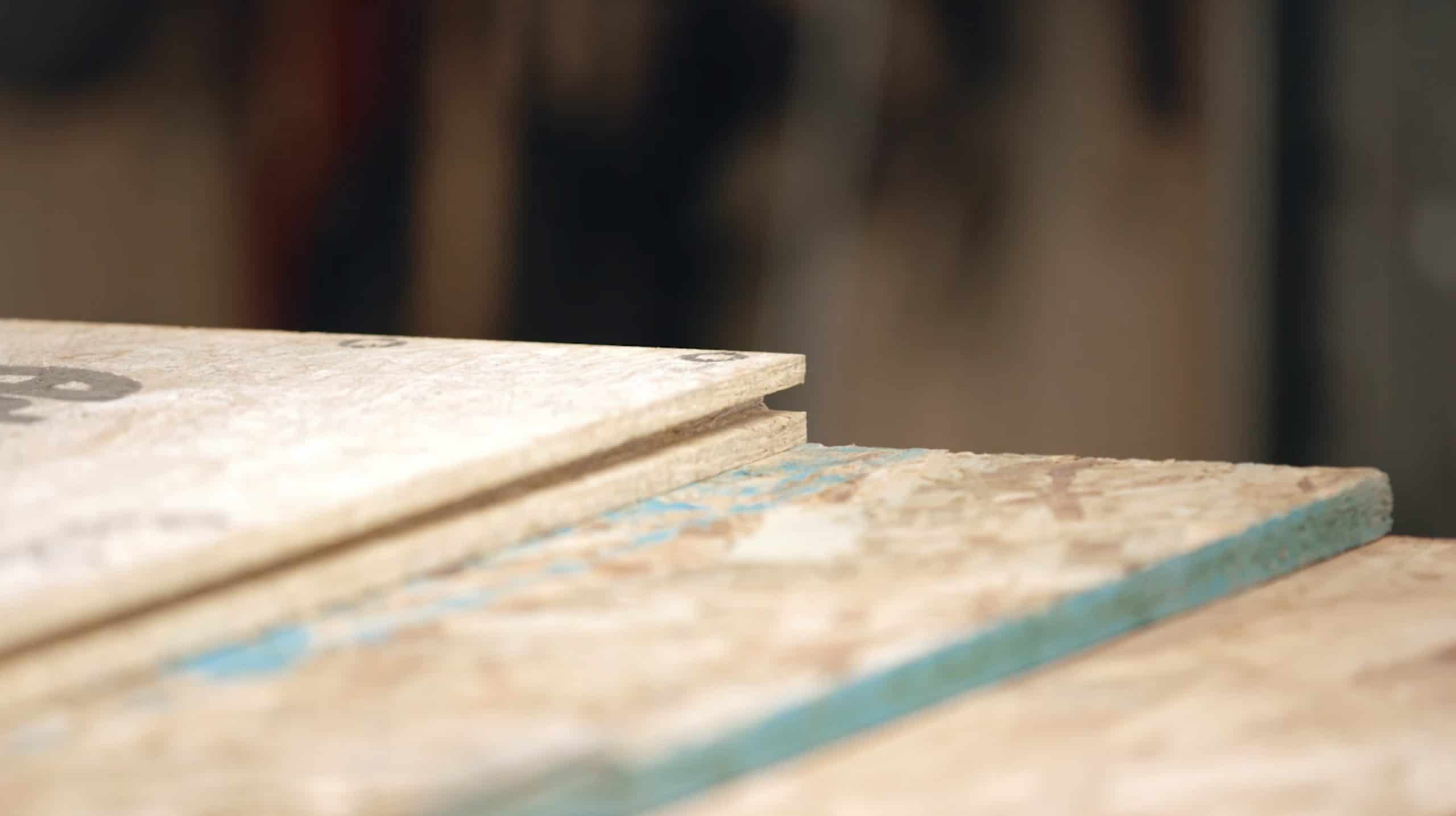
4. Plywood
A sheet good manufactured from thin layers (or “plies”) or wood veneer that are glued together. Plywoods have several benefits to builders, since they are made by binding resin and wood fiber sheets to form a composite material whose “cross graining” property provides dimensional stability and makes the strength of the panel consistent in all directions.
Remember to gap all of your ends with plywood, because it does still expand and contract with moisture.
Engineered wood boards are generally made from the same hardwoods and softwoods used to manufacture lumber, but mixed with additives like adhesives. This type of wood often utilizes waste wood from sawmills, and are treated through chemical or heat processes to produce wood that meets size requirements that are hard to find in nature.
Engineered wood is used in a variety of applications, from home construction to commercial buildings to industrial products.
“Engineered lumber is lumber that although it comes from wood, it’s been processed to be something slightly different and perform in a different, oftentimes better way than what just the raw wood would perform.” -Professional builder Jordan Smith
7 Popular Types of Engineered Wood
Engineered wood products are available as framing members—beams, for example—and sheet goods, which can be used as sheathing or flooring.
1. Laminated Veneer Lumber (LVL)
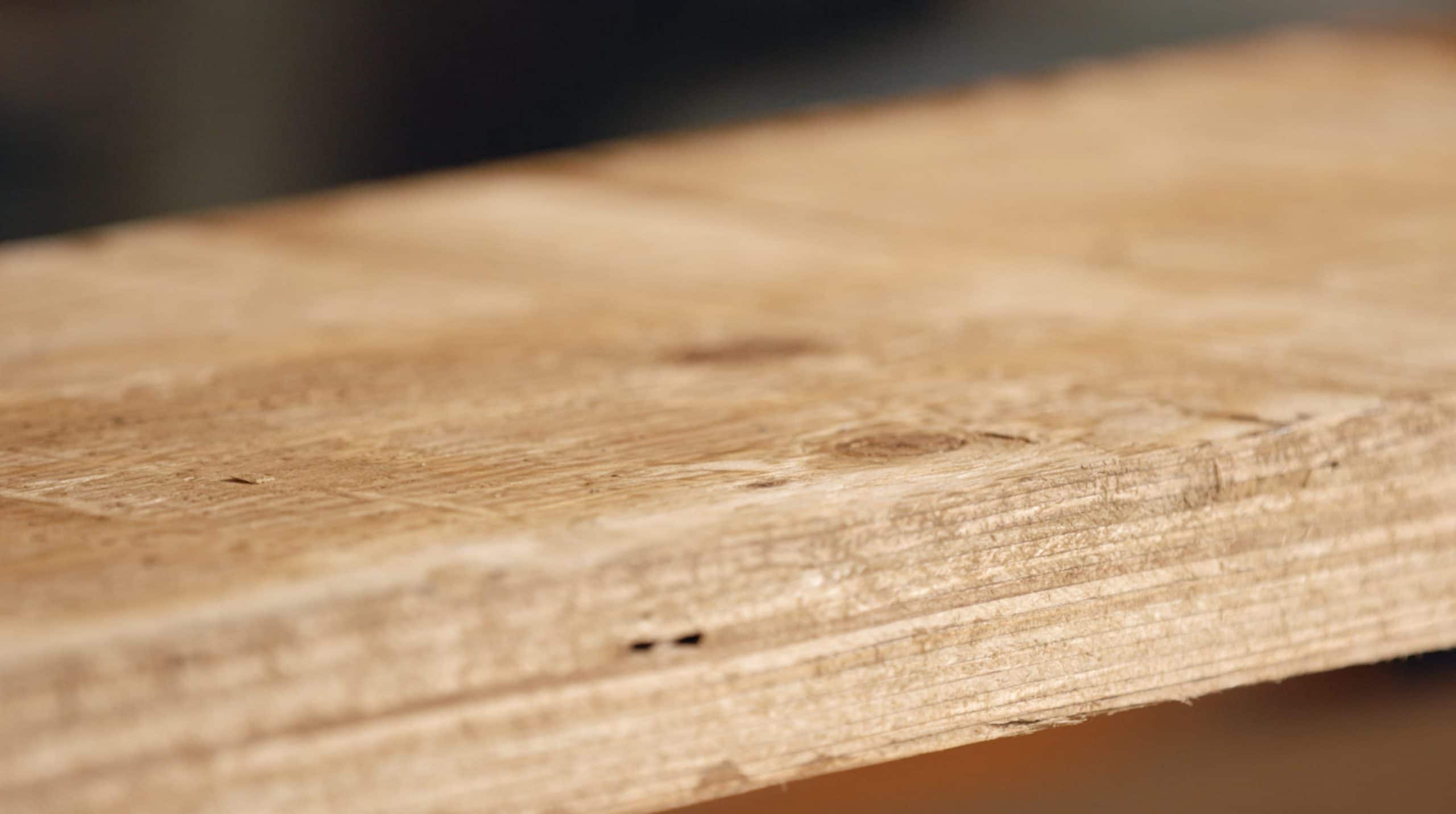
Made of wood veneers that are compressed together with resins and glues, LVL is a high density engineered wood product used in framing. LVL is very strong, but has only one strength axis, because its veneers are stacked with the grain running in the same direction. This means you can only load LVL in one direction.
2. Laminated Strand Lumber (LSL)
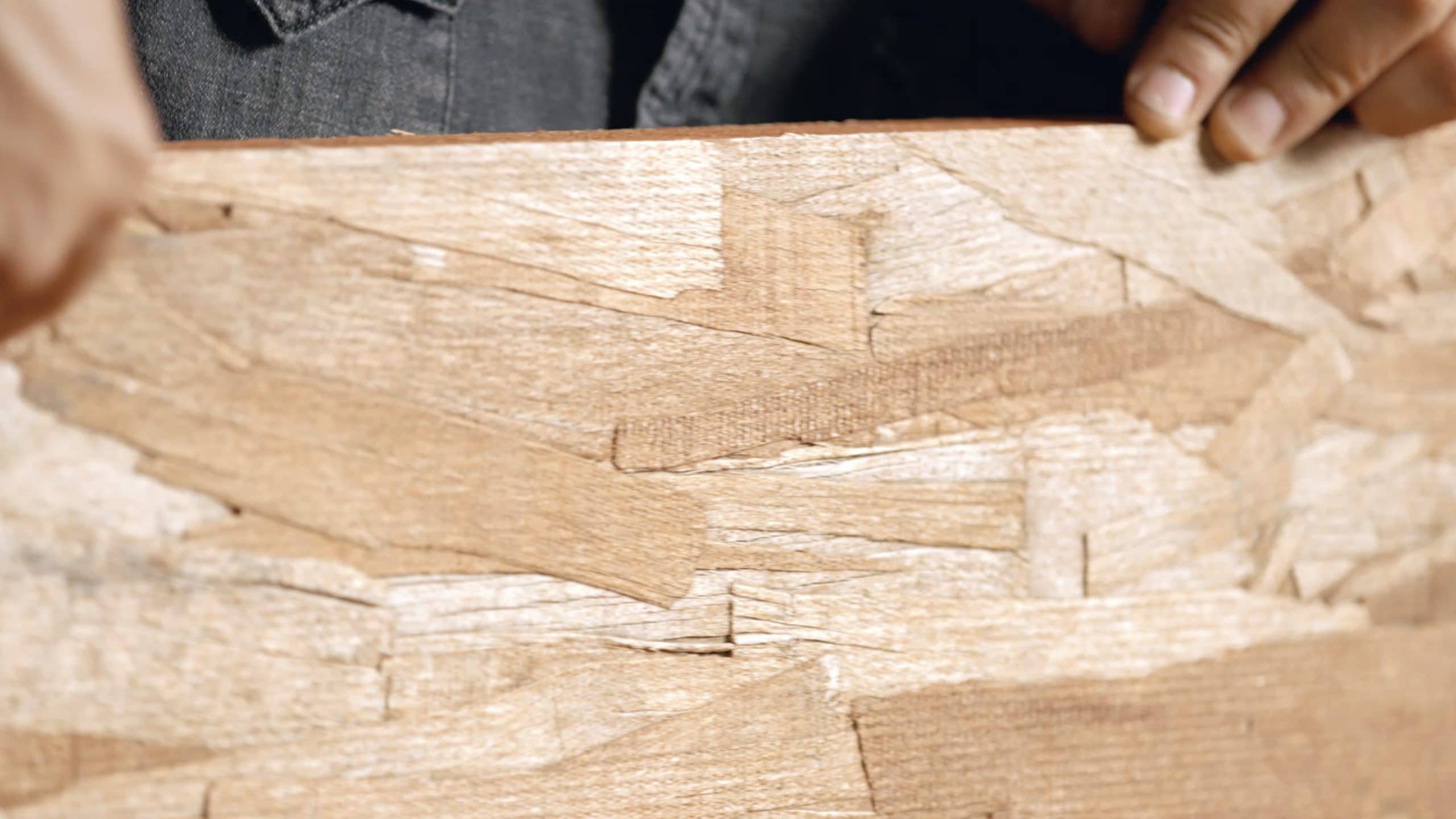
Made of small strips of wood—strands—that are placed in a dense, angled pattern, LSL is a high quality engineered wood product that can be an even higher density and stronger than LVL. It is composed of about 95% wood fiber and 5% resin. LSL is very resistant to weight and torsion because of the angled pattern in which the wood strips are placed. LSL is also expensive—it’s about 3x the cost of dimensional lumber.
3. Oriented strand board (OSB)
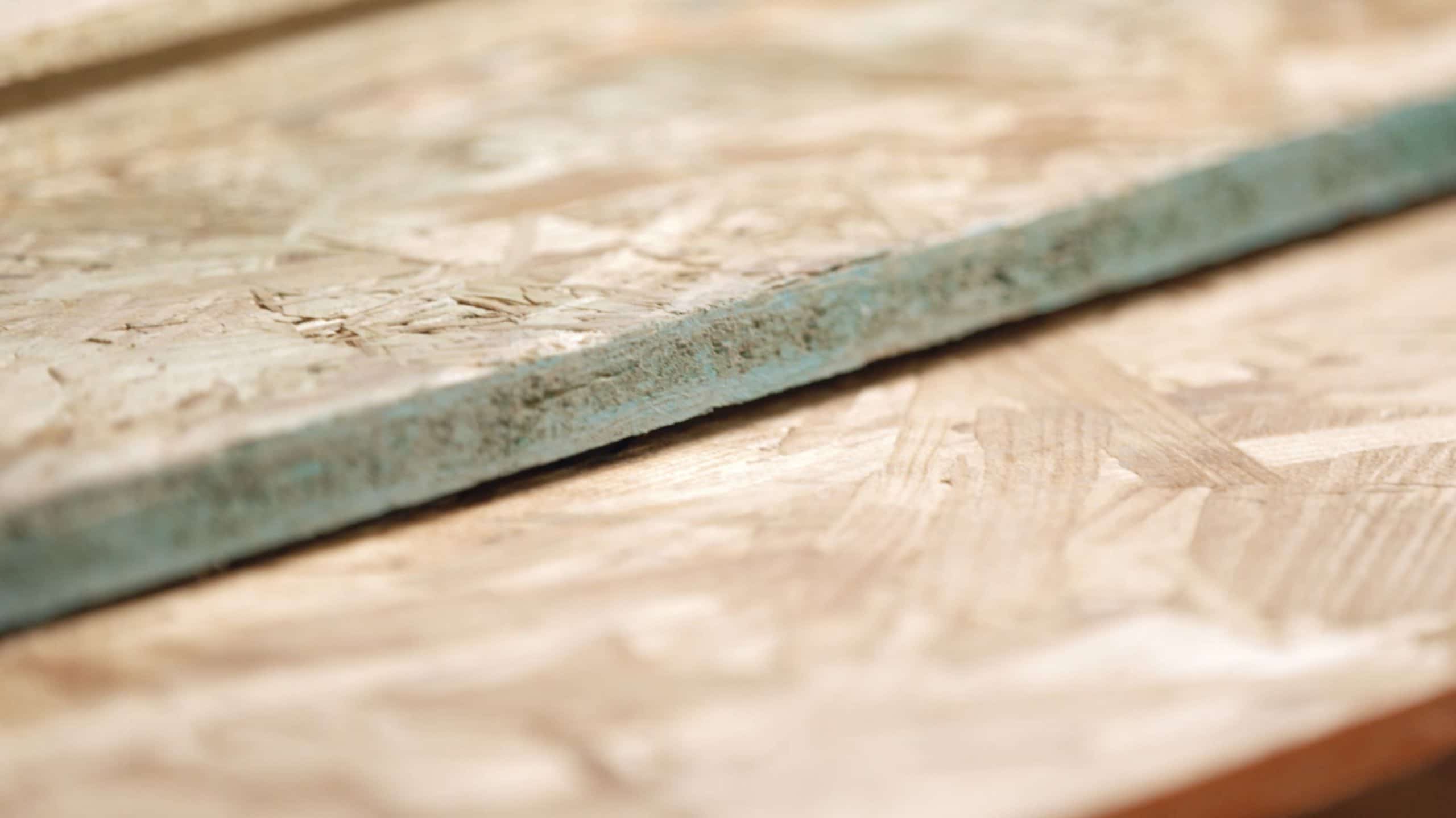
This type of sheet good is formed by combining wood strands or flakes with adhesives and then compressing them. It is manufactured in wide mats and is good for load-bearing applications such as flooring and roof decking. All OSB isn’t created equal—some is sanded (like Advantech or Legacy premium subfloor), and other boards are not. Some OSB is moisture resistant, other boards are not. Make sure that you are using premium grade OSB if there’s any chance of it experiencing whether.
It is important to note that for OSB (and plywood), you want to gap all of your ends, so that when it expands and contracts with moisture in the long direction, you aren’t causing it to buckle. However, on the tongue and groove of premium subflooring, there is a pre-manufactured stop that gives you the ⅛-inch gap in between boards.
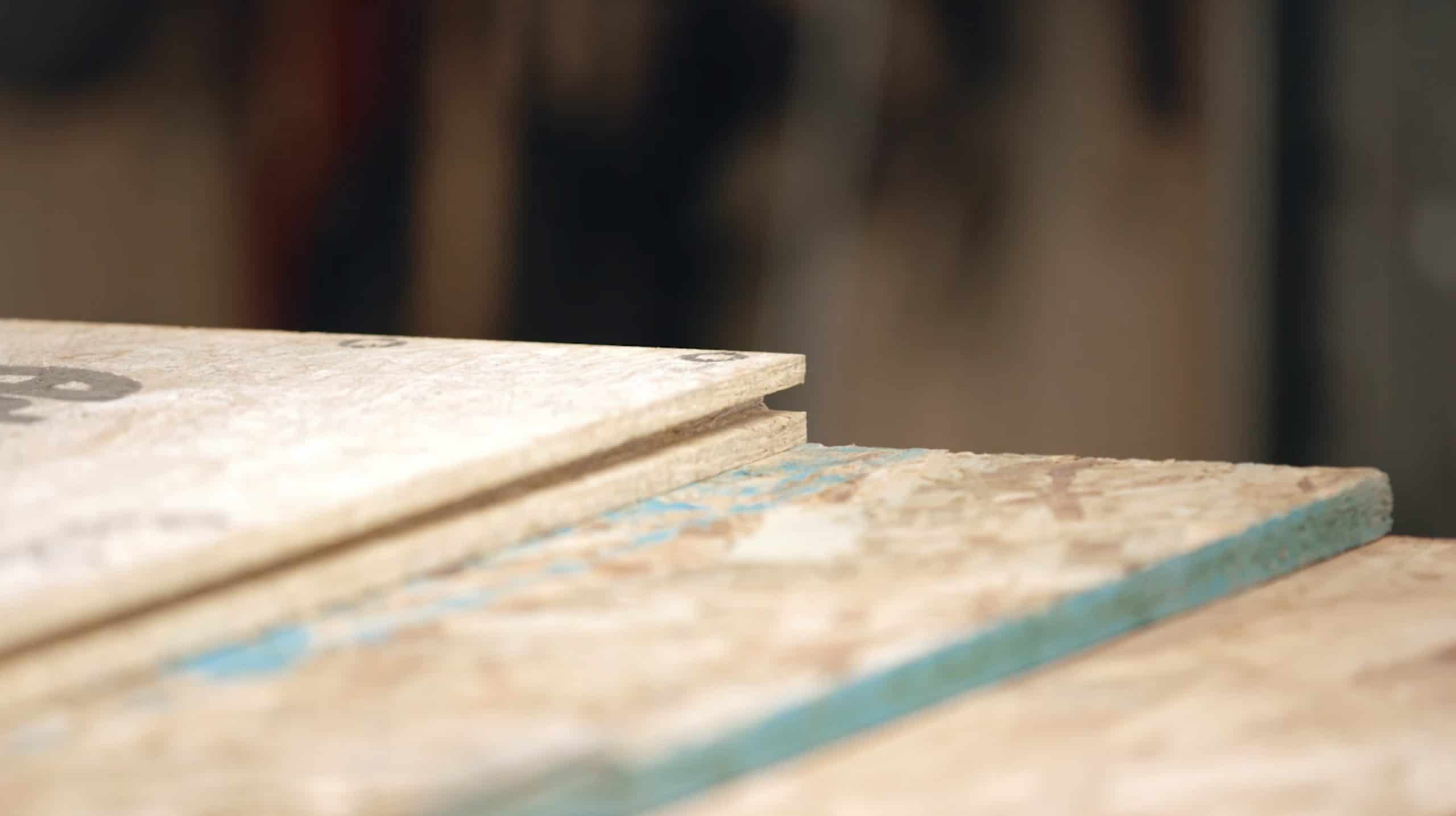
4. Plywood
A sheet good manufactured from thin layers (or “plies”) or wood veneer that are glued together. Plywoods have several benefits to builders, since they are made by binding resin and wood fiber sheets to form a composite material whose “cross graining” property provides dimensional stability and makes the strength of the panel consistent in all directions.
Remember to gap all of your ends with plywood, because it does still expand and contract with moisture.
A plywood sheet has two face veneers, so if you see a sheet graded as “AB” that means it is A-quality on one side and B on the other.
- A: This is the highest quality plywood with a smooth surface free of knots and repairs.
- B: This grade is largely free of knots, though some tight ones (under 1 inch) are acceptable.
- C: C grade plywood may include knots up to 1.5 inches and knotholes under 1 inch.
- D: The lowest grade can have knots and knotholes up to 2.5 inches. In general, any defects have not been repaired with D grade plywood.
- X: An X is used to indicate exterior plywoods. A grade of CDX would mean a plywood is C grade on one veneer, D on the other, and designed for outdoor use.
5. Medium density fiberboard (MDF)
MDF is made by breaking down hardwood and softwood pieces into fibers, which are combined with wax and resin binders, and formed into panels by applying high temperatures and pressure. It is usually more dense than plywood, and is more dense than oriented strand board, but just like OSB, there are grades that can withstand water and weather and other grades that cannot.
6. Composite board
This engineered wood term includes MDF and oriented strand board. It refers to a wood engineered with both plastic content and wood fiber that has been extruded and heated. It’s also known as engineered wood. It is easy to install, cost-effective, and good for incorporating into sustainable design, since it can be made of recycled material using fewer trees.
7. Cross-laminated timber (CLT)
This wood panel product is made from gluing together layers of solid sawn lumber. It is strengthened by layering each board perpendicular to the next and glued on the wide faces of each board. The thicknesses of the panels can easily be increased, which makes it a design-flexible material. It can be a good insulator, since it’s made of multiple layers of wood.
Learn all about the properties of wood and how wood is used in construction in the MT Copeland course on Wood Materials. Taught by professional builder Jordan Smith, the course covers topics that range from I-joists to shear strength.
Pros and Cons of Engineered Wood
“Engineered beams are a great way of getting the strength while keeping the cost and size low.”-Professional builder Jordan Smith
Advantages of engineered wood over solid wood
Engineered wood has become a popular type of flooring because of its many advantages.
- Engineered wood is sustainable, because it allows you to achieve (or exceed) the same density and strength of old growth timber, but with lumber made from young trees. It also reduces waste, because it uses all parts of the tree—even defects or pieces leftover from cutting dimensional lumber.
- Engineered wood can be stronger than dimensional lumber because of its high density and layers of grain running in different directions.
- Engineered beams come in almost any size—you can get bigger members because they’re created by composite, rather than having to be cut from single trees.
- Some engineered wood can resist warping and splitting more than dimensional lumber.
Disadvantages of engineered wood over solid wood
- Engineered wood is often less aesthetically pleasing than real wood, because of the visible wood strips (rather than the clean, natural look of solid timbers). One exception to this is architectural-grade glulam.
- Engineered wood—especially LSL—can be much more expensive than dimensional lumber.
MT Copeland offers video-based online classes that give you a foundation in construction fundamentals with real-world applications. Classes include professionally produced videos taught by practicing craftspeople, and supplementary downloads like quizzes, blueprints, and other materials to help you master the skills.